This article is a summary from the Future of Manufacturing roundtable, hosted in March in collaboration with Airbus, Irwin Mitchell, HDR, Make UK, NCC Group and Salesforce.
By investing in digital technologies, manufacturers can access business-critical data, protect their employees and become more cost-effective and sustainable.
In today’s world, data is king. All companies need access to high-quality data to properly understand their customer base, optimise their services and supply chains, innovate products and, crucially, become more sustainable. Manufacturers are no exception.
To ensure they have the best data, manufacturers must go on a digital transformation journey, insists Jermaine Benson, Regional Sales Director at global customer relationship management software company, Salesforce. He stresses, however, that there is often too much focus on the technology itself.
“At the moment, we hear buzzwords like ‘AI’ and ‘machine learning’,” he says. “This type of technology is just an enabler that helps a firm achieve the outcome it wants. Ultimately, tech drives better use of big data so that companies can make the right decisions for themselves, their customers and their employees.”
Preventative maintenance and health and safety improvements
The right technology can streamline operations and save a business money. For example, aircraft manufacturer Airbus has developed an aviation analytics platform that enables airlines to intervene before an issue occurs on an aircraft. “Previously, we only had the ability to replace a component on an aircraft once it had failed” explains Mark Crompton, Global Head of Employer Marketing and Employer Branding at Airbus.
“But now, we can monitor the behaviour of all components on our aircraft at the same time and replace them just before they fail and at a base convenient to the airline. This type of preventative maintenance is more efficient for planning and supply chain management, and it changes the way we use aircraft and schedule flights and routes.”
In an uncertain world, tech innovation
can future-proof businesses.
In hazardous areas of manufacturing, technology can have a transformative effect on health and safety. “PPE is usually a hard hat and a hi-vis jacket,” says Richard Papworth, Director of engineering, architecture, environmental and construction services firm, HDR. “Some people might think: ‘How is that going to protect me?’ Actually, if that PPE is connected to the Industrial Internet of Things (IIoT), it can prompt an alarm or shut machinery down if workers get too close to a dangerous area.”
In an uncertain world, tech innovation can future-proof businesses. Verity Davidge, Director of Policy at Make UK — an organisation representing and championing UK manufacturers — notes that firms that had significantly invested in digital technologies were better able to weather the pandemic. “It meant they could, for example, start offsite production and operate machinery away from the manufacturing shop floor,” she says.
“It’s easy to underestimate how effective industrial digital technologies can be and the economic advantages they bring. Some smaller companies may be put off by the cost — but our data shows that it can offer a return on investment in less than three years.”
Barriers to tech adoption and importance of moving to the cloud
Apart from cost, there are other barriers to tech adoption. Manufacturers might be put off from investing in the latest robot technology if skills and labour shortages made it difficult to find robot maintenance engineers. And staff can be suspicious of new technology, believing it can put jobs at risk.
The main stumbling block, however, is cybersecurity risk, particularly if operational technology systems (such as fridges or conveyor belts) are connected to information technology systems. “It’s true that this increases your attack surface,” says Tim Rawlins, Senior Adviser to global cybersecurity and risk mitigation company, NCC Group.
“Manufacturing is looking to achieve net zero, and for that, it needs big data to become more efficient and effective. So, yes, operational technology and IT need to be connected — but always with safety and security in mind.”
Giving cybersecurity over to an external party by moving operations into the cloud may seem counter-intuitive, agrees Rawlins. “Although, from an economic standpoint, a business should at least consider it,” he says. “Because if you aren’t moving into the cloud, then you’re not undergoing digital transformation.”
In collaboration with
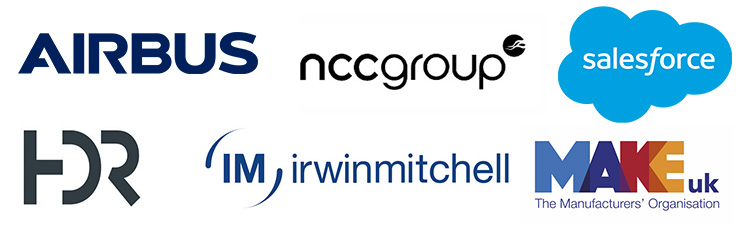