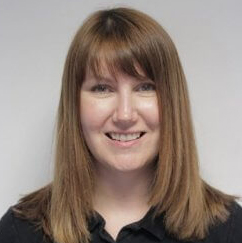
Philippa Glover
Managing Director, CNC Robotics
Machining with robots is becoming an increasingly popular option for the manufacture of large, complex items across a wide range of materials and applications.
The future of robotics and automation is being led by innovative companies who are supporting UK manufacturing by developing solutions that not only enhance productivity but also improve businesses competitiveness.
It is widely recognised that manufacturers are facing challenges in an increasingly competitive landscape. Productivity is being highlighted as a major issue as well as the growing skills shortage. Whilst the UK Is behind the other G7 nations in terms of the number of robots deployed we are starting to see change. Manufacturers are turning to robotics and automation as it is often a more cost-effective approach and can offer increased production output. Although the automotive industry has pioneered the use of robots, applications have been developed across all sectors. There are many cases where the main challenge is an extreme working environment that restricts the use of manual methods or conventional machine tools. Robots are, of course, able to operate in more extreme conditions than humans but they are also more tolerant than many machine tools. They are less susceptible to extremes of temperature and humidity, and are often more resistant to dust or other contamination, making them less prone to problems in challenging manufacturing environments.
Machining with robots
Machining with robots is becoming an increasingly popular option for manufacturers especially when producing larger parts in plastic, foam, composites and softer metals. Systems developed have been used to replace many hand-finishing tasks, where robots can provide a faster and more consistent approach than manual operations and eliminate health and safety issues. A growing number of software companies now support the programming of robots with variants of their five-axis milling capabilities. The combination of the robot and the software gives the equivalent benefits to those gained when programming machine tools, including the ability to create toolpaths directly from CAD models, together with options to simulate and optimise the programme on the computer. These options help to ensure that the robot will operate efficiently and safely, giving the desired productivity across all types of manufacturing.
Robotics In the creative industry
As with other industries, the key to the success of robot machining has been the ability to produce larger items more quickly and more consistently than traditional manual methods. In addition to the manufacture of film and theatre props, applications include making installations for theme parks and museums, and even carving decorations in ice for the Ice Hotel.
Eliminating health and safety concerns
As well as being able to produce complete items, robot s can undertake a variety of finishing operations. Using robots gives greater consistency than manual trimming as well as being quicker in most cases. Reliability can be further enhanced by fitting the robot with an inspection probe initially to ensure that the part is in the correct position before cutting starts. In addition, using robots eliminates the health and safety concerns resulting from demanding and repetitive manual operations.
Bespoke applications
The flexibility of robots combined with broad experience, means that companies at the forefront of innovation, can develop bespoke applications for projects where conventional machine tools are unable to provide a cost-effective solution. The systems developed often involve a single robot undertaking multiple operations or a series of robots carrying out different stages of the overall process. Successful applications include the use of robots to manufacture temporary storage options during house repairs, to carve ice sculptures and to braid composite fibres for the production of camera tripods.
Whether the problem is an unusual material, a demanding environment or particularly complex geometry, robotics companies with the experience behind them can work with the customer’s staff to pave the way and develop innovative approaches to solve complex manufacturing challenges.