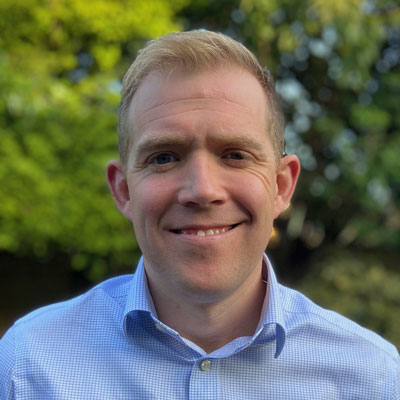
Ben Morgan
Research Director, the University of Sheffield Advanced Manufacturing Research Centre (AMRC)
Model-based systems engineering creates a digital thread between the concept design stage of a product and the end of its life, and it’s a more sustainable manufacturing approach.
If the UK is to meet its 2050 net zero commitments, manufacturers will need to think differently about their products and processes. In one way, this is incredibly daunting, admits Professor Ben Morgan, Research Director at the University of Sheffield Advanced Manufacturing Research Centre (AMRC), part of the High Value Manufacturing (HVM) Catapult, which develops innovative solutions to industry’s biggest challenges.
Model-based systems engineering in products
It’s also exciting because it can lead to the adoption of cutting-edge innovations such as model-based systems engineering (MBSE). This theme — a key focus of the centre’s research and development strategy — is generally used in the design of complex, high-value manufacturing products in highly regulated sectors such as aerospace, maritime and nuclear energy.
“Model-based systems engineering is set to replace the current archaic document-centric approach, where 2D design drawings are printed out and sent to the shop floor,” says Professor Morgan.
“With MBSE, design engineers, manufacturing engineers, supply chain stakeholders and the end customer use a common complex digital model as the primary means of information exchange and feedback. This helps to create a digital thread between the concept design stage of a product and the end of its life.”
If everyone can access the same digital model at the
same time, each team can see those changes
being made in real time — from anywhere.
Advantages of model-based systems engineering
Computer-aided design (CAD) has enabled better data sharing between different stakeholders for some time. However, CAD is just one part of the bigger digital MBSE picture. “The simulation and modelling capabilities we have now are more advanced than ever,” explains Professor Morgan. “Plus, the advent of Industry 4.0 has increased machine-to-machine connectivity, which means huge amounts of data can be captured on the shop floor and fed back into the model.”
There are two major reasons why model-based systems engineering offers a more sustainable approach. First, it compresses the lifecycle of the concept design stage. Traditionally, competing interdisciplinary manufacturing teams working in different locations have had to indicate changes to a product over email or during meetings. If everyone can access the same digital model at the same time, each team can see those changes being made in real time — from anywhere.
Secondly, while it’s relatively easy for manufacturers to understand the scope 1 and 2 emissions they create within their factories, it’s harder to get a handle on the scope 3 emissions in their upstream and downstream supply chains. “Model-based systems engineering provides a platform to enable carbon accounting,” says Professor Morgan. “It allows manufacturers to track the carbon of the parts they are using through the supply chain in an interoperable and standardised way.”
Centralised data offers ‘a single source of truth’
The centrality of data also plays a key part in AMRC’s sustainability strategy. It has developed an open-access digital architecture for manufacturing shop floors called Factory+. This can capture data — on everything from smart plug sockets to furnaces — and bring it all together in a centralised system. By offering a ‘single source of truth’, manufacturers can make more informed decisions about efficiency and sustainability.
The centre is keenly focused on the sustainability of its own day-to-day processes, running in-house energy-saving initiatives and working with industrial partners to share best practices. It will also continue to innovate for its customers in the net zero technology space.
For instance, it is opening a £50 million open-access research facility, which will be home to Composites at Speed and Scale (COMPASS) to solve composites manufacturing challenges for the aviation industry. The first research programme to take place in the facility will be the Isothermic High-Rate Sustainable Structures (IHSS) project, led by aerospace giant Boeing, in partnership with AMRC, Loop Technology and Spirit AeroSystems.
“Net zero is a weighty target that, for some sectors, is a mountain to climb,” says Professor Morgan. “We want to help them by bringing new emission-reducing technology and net zero products to market as quickly as possible.”