This article is a summary from the Future of Manufacturing roundtable, hosted in March in collaboration with Airbus, Irwin Mitchell, HDR, Make UK, NCC Group and Salesforce.
To help address skills shortages, manufacturers must understand the competencies they’ll need in the future and establish long-term relationships with schools and universities.
The manufacturing sector is struggling to close a sizeable skills gap. According to research from Make UK — the organisation that represents and champions UK manufacturers — there are 77,000 live vacancies in the industry. Yet, 36% of manufacturing vacancies are proving hard to fill as applicants lack the appropriate skills or experience.
“To be fair, skills and labour shortages are a global problem, not just a UK one,” argues Richard Papworth, Director of HDR. “Getting school leavers into manufacturing is key — although that’s a challenge because there’s a perception that the industry is not a good place to work. So, it’s vital to show what a career in manufacturing can really offer. I’m passionate about what I do in construction. We have to make young people similarly enthusiastic about manufacturing.”
Building long-term relationships with education partners
In a way, that should be easy because manufacturing has a great story to tell, says Verity Davidge, Director of Policy at Make UK. The sector drives over 60% of all UK research and development, is responsible for the majority of UK exports — and the wages it pays are above average.
However, she agrees that the sector must do more to sell itself as an exciting career choice. “The companies we represent are doing important work, such as providing the answers to climate change or creating ventilators during the pandemic,” she says. “Yet, we are struggling to attract talent — particularly, diverse talent — so we need to be honest with ourselves about that. It’s why we’re running a National Manufacturing Day on September 28 and asking manufacturers to open their doors to local communities and colleges. We must show what the sector does so that we can attract the next generation — and older unemployed people who may be unaware of job opportunities at their doorstep.”
Manufacturers who modernise will be better placed
to attract the next generation of skilled workers.
Mark Crompton, Global Head of Employer Marketing and Employer Branding at Airbus, thinks there are two things that big businesses can do to get a handle on the problem. “The first is better forecasting to understand the skills and competencies organisations will need in the future,” he says. “The second is to establish long-term relationships with schools, universities and other education partners. At Airbus, we run outreach and liaison programmes with local schools and communities where we work with children to enhance their STEM education. For students, we run on-campus activities, career fairs and research projects.”
Transforming skills by levelling up opportunities
Claire Petricca-Riding, Partner and National Head of Planning and Manufacturing at Irwin Mitchell, believes there is a wider issue to consider. “It involves government policy and intervention around levelling up,” she says.
“When we talk about levelling up, we often mean building houses or roads. However, it’s more than that. It’s about how we transform society to be more productive and, for me, that starts with levelling up education. We have to bring forward digital transformation and make it a basic right for all young students to have access to the internet in a safe and secure environment where they can learn and transform their skills. We also have to entice older workers into the sector with upskilling initiatives.”
Manufacturers who modernise will be better placed to attract the next generation of skilled workers, says Jermaine Benson, Regional Sales Director at Salesforce. “Generally speaking, younger industries have a younger demographic and high investment in technology initiatives,” he explains.
“It’s the opposite with manufacturing: it has a higher median age workforce but lower investment in technology initiatives. We should get the message across to firms in the sector that if your objective is to be a digital-first business with a focus on net zero, then investing in technology is a great way to make manufacturing in the UK the gold standard — and attract talent.”
In collaboration with
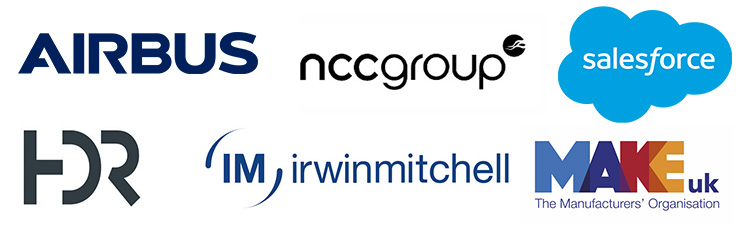